-
Over 90 Years
industry expertise
-
Largest
facility & product range
-
Leaders
in the technology market
-
UK Based
service department
Caddy
The CADDY horizontal mechanical shears have distinguished themselves throughout the world due to their extreme high productivity and corresponding low cost per slug. The horizontal shearing action allows easy clearance compensated angle shearing to virtually eliminate shear face angularity. The CADDY produces the highest dimensional accuracy possible to fully utilize today's net and near net forging technologies.
FICEP as the leading manufacturer of Forging equipment are also famous for our billet shear “The Caddy” developed with new electronic components and special accessories.
The final goal for which the entire forging industry is striving, is to reduce production costs and improve the product quality, this is shown in the tendency to use more and more frequently closed-die forging processes to eliminate flashes, with a consequent material and energy saving, and producing a near zero shaped part.
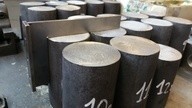
Close-die Forging Demands
The must for the closed die forging is to use slugs having the volume (weight) included within strict tolerances. However, some fundamental conditions have to be met in terms of machinery, tooling and material for the slugs to be suitable for the subsequent forming process. Good shear quality and weight tolerances within ± 0.3 % can be achieved only if these requirements are fulfilled. Some very specific and exacting demands are made by the forging industry in respect of the quality and quantity of bar stock or billet slugs for hot or cold forming.
Actual Shearing Features
Sheared slugs must be of constant volume, good squareness, display minimum distortion, and be devoid of shearing faults. Besides these specific shearing requirements, high output, minimum set-up time and fully automatic work-cycles are the major features of a high performance modern shearing line. Bar stock and billet shears are today an established feature of forging and forming plants for the economical production of such slugs. The machines are linked to feeding and discharge equipment to create automatic solutions.
CADDY | CADDY 28 | CADDY 50 | CADDY 52 | CADDY 56 | CADDY 63 | CADDY 70 |
---|---|---|---|---|---|---|
Cutting force [kN] |
320 | 900 | 900 | 1400 | 2200 | 3000 |
Max stroke per minute [no.] |
120 | 50 | 100 | 78 | 70 | 70 |
Round (min/max) [mm] |
32 | 64 | 52 | 56 | 63 | 70 |
Square (min/max) [mm] |
- | - | - | 50 | 55 | 65 |
Clutch & Brake type |
Pneumatic | Pneumatic | Hydraulic | Hydraulic | Hydraulic | Hydraulic |
Main motor power [kW] |
5.5 | 11 | 15 | 22 | 30 | 37 |
CADDY | CADDY 80 | CADDY 90 | CADDY 100 | CADDY 140 | CADDY 160 | CADDY 180 |
---|---|---|---|---|---|---|
Cutting force [kN] |
4400 | 5000 | 6000 | 8000 | 11500 | 14000 |
Max stroke per minute [no.] |
63 | 60 | 56 | 38 | 33 | 33 |
Round (min/max) [mm] |
80 | 90 | 100 | 140 | 160 | 180 |
Square (min/max) [mm] |
75 | 85 | 100 | 135 | 160 | 180 |
Clutch & Brake type |
Hydraulic | Hydraulic | Hydraulic | Hydraulic | Hydraulic | Hydraulic |
Main motor power [kW] |
45 | 55 | 75 | 110 | 160 | 200 |
FULLY AUTOMATIC SHEARING LINES
Caddy Shearing Lines
The design, construction, devices and controls of FICEP Caddy shearing lines make them ideally suitable for operation under harsh plant conditions. They incorporate the major features of a high-performance shearing line:
- high output minimum maintenance
- minimum set-up and handling times
- automatic work cycle
- rugged design
- high rigidity
- wide range of high-tech accessories: weighing system, laser measurement, chamfering unit, etc
Modular Design
The proven, modular design system enables virtually all practical needs to be met. The standard layout that has evolved from consistent collaboration with the forging industry shearing lines and operate at high speed to achieve maximum output.
Feeding System
- The feeding system for processing round and square bars consists, most of the time, of a V-loader and conveyor. A bundle of bars is placed on the V-loader. Here, the bars are automatically scrambled and then discharged by a hydraulic kick-off mechanism gently, and with a minimum of noise, onto the feed conveyor.
- A maintenance-free and reliable hydraulic motor powers the conveyor. This drive system is designed to provide various different conveyor speeds as well as acceleration and braking.
- A complete range of different unscramblers is available for particular demands (i.e. very small diameters of 5 mm or very long bars as 24 m).
Trim Cut and End Bar Rejection
- The shearing machine processes the bar in automatic work-cycle with the first off-cut of each bar (the trim cut) and the trailing end slug being segregated in the discharge chute.
- If required, the system can be expanded to include either manual or automatic discharge of a sample slug for weight checking purposes.
Horizontal Shearing Action
- The shearing action is in the horizontal plane with the shear force generated by the flywheel, eccentric shaft, ram and slide. The stationary shear blade is mounted in a solid, cast steel frame, which, together with the machine frame itself, and the guides, serve to create a rigid and sturdy unit.
- This innovative design ensures that the forces created during the shear stroke are distributed over the whole frame limits. The components located in the force flow and subject to high stress, such as the ram and shear slide, are forged.
- The flow of the material grain is configured such that the components are able to withstand high degrees of stress guaranteeing maximum security against fracture.
- Ruggedness, and reliable operation, in everyday practice have proven a high reliability of the design concept of the machine.
- For a complete machine safeguard, an electronic stress control device is also available, with display of the same at every working cycle.
- The bar and slug clamps, as well as the infinitely variable blade clearance, are fundamental for achieving the quality of slug referred to previously.
- The performance levels of a shearing are, amongst others, reliant upon set-up times.
- Bar feed and clamping operations are performed at extremely high speed since they must take place during the short, return idle stroke of the shear. Besides a higher machine productivity, this cycle allows to increase the clutch life, since it would only intervene at the beginning or end of each bar and not at each cut.
- For long pieces, a single shear cycle is available.
- The machine automatically chooses the continuous cycle whenever this is possible, thus always ensuring the maximum productivity.