-
Over 90 Years
industry expertise
-
Largest
facility & product range
-
Leaders
in the technology market
-
UK Based
service department
Close Coupled Drill and Saw Systems
A close coupled drill and saw machine used for steel fabrication combines a drill and saw positioned side by side. This type of tandem system is ideal for many steel processors as it reduces the plant space required, needs only one operator, and reduces investment costs compared to buying separate drilling and sawing machines, unless the facility has unlimited space.
- Each spindle has a secondary axis of 300 mm so holes on both flanges and the web that do not share the same length coordinate can be drilled simultaneously.
- Underside scribing can also be added to permit scribing on four surfaces simultaneously.
- Requires less than half the space of a conventional split system
- Smaller capital investment
- Single operator
- The drill operator no longer waits for the saw operator or vice versa
- Multi tasking software permits the sawing of one section while drilling of a different size section simultaneously.
- Positioning of the saw after the drill eliminates the minimum length finished part that can be off loaded on the exit side of the system.
- One common CNC control with onboard software, controls all of the functions of the saw and the drill automatically. It is not necessary to manually stop / start the sawing process once the section is in position.
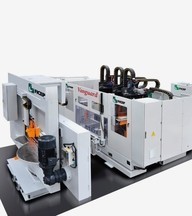
CNC Controlled Band Saw
- The Ficep engineered and manufactured band saws have a movable magnet integrated into the design. Trim cuts, short parts and drops are automatically unloaded without operator involvement.
- The position of the blade relative to the section being processed and is automatically controlled by the software. This determines the start position, when to slow down for the web and the end of the cut
- When a new blade is installed, the system automatically runs-in the blade to achieve the optimum blade life.
- All adjustment of the horizontal clamp positions and the blade guide position is established automatically through the software even on miter cuts.
- When the saw blade requires replacing the operator is notified on the CNC.
- Automatic sensing of blade pinching in the beam due to material stresses provides less traping of the blade.
- Automatic separation of the cut part from the stock length prior to the blade withdraws to enhance blade life.
- PC based control system for ease of operator familiarisation
- Low maintenance cost due to the utilisation of a standard PC platform
- The Ficep software eliminates the requirement for additional hardware such as third party axis control boards, PLC hardware and encoder switching boards
- The Ficep Windows based control is provided with the proprietary Ficep software for remote diagnostics through a phone or internet connection.